Do you have a steering or handling problem that nobody seems to know how to fix? Or a wheel that nobody can balance? Or a weird vibration that won’t go away? It might be a bad tire or a bent wheel!
Most tire manufacturers today have a pretty good grip on quality control, and perform extensive tests to weed out tire defects that may occur in manufacturing. Tires are a hand-built product that requires skilled labor. Mistakes sometimes happen, though, and tires that are less than perfect sometimes slip through the screening process. So if you have recently replaced your tires and are now having a steering, handling or tire-related problem, it could be a bad tire.
The more difficult situations to diagnose are those where an existing set of tires may be causing a problem. The underlying cause may be a manufacturing defect that took time to make itself noticeable, or it could be the result of structural damage to the tire caused by a pothole or improper mounting.
If you suspect a tire problem, inspect the tires carefully for obvious tread or sidewall defects such as cuts, bulges, ripples, bruises, scrapes, missing chunks of tread, separations, cracks, etc. Uneven tread wear may indicate misalignment, under or overinflation or a tire construction defect.
Tire defects that can cause a steering pull or vibration may not be visible to the naked eye because they are inside the tire. This includes defects such as off-center belts, misplaced belt splices, damaged belts or cords, or beads that are in different planes as well as variations in sidewall stiffness (force variation).
TIRE CONICITY PROBLEMS
When a tire is being built, the belts must be almost perfectly centered. According to some tire manufacturers, a belt that is out of position more than one millimeter may cause a steering pull on some vehicles. The position of the outermost belt is the most important because it has the greatest effect on directional stability.
A tire with an off-center belt will lead to one side because the location of the belt shifts more weight to one side of the tread than the other. This condition is known as a “conicity” problem, and occurs because the tire behaves as it if were cone-shaped. A cone always rolls in a circular path towards the pointed end. A conicity pull will therefore always be directional (either to the left or right), and can be reversed by switching the front tires from side to side, or by mounting the offending tire backwards on the rim.
Conicity problems can also arise when the beads are not in the same plane. The resulting difference in sidewall height and loading will create the same unbalanced steering forces that make the tire want to roll towards the shorter side.
Conicity problems are usually most noticeable on the front wheels, but may affect tracking and induce some rear axle steer on vehicles with independent rear suspensions. Vehicles with less caster also seem to be more sensitive to conicity probably because high caster angles have a stabilizing effect on the steering.
If you are trying to diagnose a steering pull and suspect a tire may have a conicity problem, rule out the other possibilities first. Check inflation pressure in both front tires and make sure it is equal on both sides. Low pressure can cause a pull towards the side with less pressure. Compare tire sizes and tread wear on both sides. Measure tread wear, too, because the steering will pull towards the side with the “shorter” tire (the one with the most tread wear). Also, check ride height and make sure it is within specs and is equal on both sides. The steering will usually pull towards the low side. Check for brake drag. A frozen or sticky caliper can cause a pull towards the side that’s dragging.
Next, switch the left and right front tires to see what effect it has on the steering. If the steering still pulls in the same direction, the problem is not a bad tire. It is an alignment problem. Take your vehicle to an alignment shop and have them check for camber or caster misalignment, or the presence of a rear axle thrust angle. If the direction of a steering pull changes direction when you swap the front tires, one or both front tires may have a conicity problem.
The next step would be to swap the front and rear wheels on one side (right or left) to see if it eliminates the pull. No change would tell you it is the other front tire that is causing the steering pull. Swapping the other front tire to the rear should eliminate the problem as long as the offending tire remains in the rear. But if somebody rotates the tires later on and the bad tire ends up back in the front again, the steering pull will return. Replacing the offending tire will get rid of the problem altogether, and may be necessary if the tire causes problems in the rear, too.
Another way to reduce the effect of a tire conicity problem is to increase the inflation pressure of the tire. But the tradeoff may be a harsher ride and increased center wear in the tread.
TIRE VIBRATION PROBLEMS
Though vibrations are usually caused by an out-of-balance wheel and tire assembly, it is important to remember that vibrations can also be caused by excessive radial (vertical) and lateral (sideways) runout in the tire, wheel or hub. Loose, worn or damaged wheel bearings as well as certain kinds of tread wear can also cause annoying vibrations.
When troubleshooting the cause of a vibration problem, start by inspecting the wheels. Look for evidence of missing weights, mud or dirt packed in the back of the rim or debris embedded in the tread that could create an imbalance. Also, rotate and wiggle each wheel by hand to check for excessive play or noise from the wheel bearings.
If your vehicle has alloy rims (particularly a performance or sports type vehicle), tire slippage on the rim may have thrown the assembly out of balance. This can happen if a long-lasting lubricant such as silicone was applied to the rim or tire bead when the tires were mounted. Under hard acceleration or braking, the tire may actually rotate slightly on the rim. The cure? Remove the wheels, put the wheel and tire on a tire machine and break loose both beads. Thoroughly clean both mating surfaces, then reinflate the tire to reseat the beads and rebalance the assembly.
If the radial cords in the sidewalls of a tire are not spaced evenly or are damaged, it can create a “waddle” or vibration due to force variations in the stiffness of the sidewall as the tire rotates. This condition, which is referred to as “loaded runout,” is most noticeable at low speed (5 to 30 mph), and may also appear as ride roughness at highway speeds (50 to 70 mph). A Tire Problem Detector may be needed to diagnose this kind of problem. This device has a roller that can be positioned under a tire it can be checked for spindle movement while rotating the tire slowly with the weight of the vehicle pressing down on it.
Another source of vibration can be uneven tread wear. Run your hand across the tread in both directions. If one way feels rougher than the other (like toe wear), lack of rotation may have caused a heel-and-toe or sawtooth wear pattern to develop on the tread blocks. This kind of wear is most often found on the rear tires of front-wheel drive cars. The wear may be barely perceptible to the naked eye, but is rough enough to produce an annoying vibration at medium to high speeds that feels like a bad wheel bearing. Rotating the tires once this kind of wear has developed is a waste of time because it takes too many miles to scrub off the uneven wear. Replace your tires.
Scalloped wear on a tire would tell you the tire is bouncing as it rolls along because it is out-of-balance, out-of-round or the shocks are weak.
Be sure to measure tread depth, too. Measuring tread depth at several points around the circumference of the tire will tell you if the tread is wearing evenly and if the depth is equal. A difference of more than about 1/16th inch (.0625 inches) would indicate an out-of-round condition. Most tires should probably have less than .050 inch of radial runout, and some even less depending on how sensitive your vehicle’s steering and suspension (and driver) are to vibration.
TIRE & WHEEL RUNOUT CAN ALSO CAUSE VIBRATIONS
An out-of-round condition can be confirmed by measuring radial runout on your vehicle with a dial indicator. Position the tip of the pointer against the center of the tread and slowly rotate the tire until you have found the high and low points. If the difference is more than .050 inches, there is too much runout.
If you do not have a dial indicator, the “poor man’s” alternative is to use a piece of chalk and a block of wood. Use the wood to support the chalk. Spin the tire by hand and move the chalk closer until it just touches the tire. This will mark the high spot. If the mark extends less than half way around the tire and you see an air gap between the tire and chalk that’s as wide or wider than a nickel at its widest point, the tire has too much runout.
You can attempt to correct runout by repositioning the tire on the rim to match the tire’s high spot with the rim’s low spot. If you are getting new tires on your vehicle, potential runout problems can be minimized when the tries are mounted by aligning these two spots (if the tire manufacturer provides a mark that shows where the high spot is on the tire).
On some vehicles, the low spot on the rim may be marked with a paint dot inside the rim dropwell. Ford and Chrysler do this on their steel rims. Most aftermarket steel replacement rims are similarly marked. General Motors and most Japanese vehicle manufacturers use the valve hole to mark the low spot. This is also the case on most aluminum and polycast rims as well as unmarked rims. Medium truck (20 inch or larger) steel tubeless disc wheels have a dimple or small indentation to mark the low spot on the same side of the rim as the valve hole.
The low spot on a rim can also be found by mounting the wheel on a balancer and using a dial indicator on the bead on the rim as the wheel is rotated slowly by hand. Ideally, there should be less than .040 inches of radial runout on a steel rim, and no more than .030 inches on an aluminum rim.
Once the tire high spot and rim low spot have been found, rotate the tire so the two line up. Or, if you suspect runout but don’t know where the high and low sports are and do not have a dial indicator to find them, try rotating the tire 180 degrees on the rim to see if that reduces runout. If runout is now less than specs, or the vibration has ceased, you have solved the problem. But if it still exceed specs or still shakes at speed, you have to make a decision.
A tire with too much runout can be buffed or shaved on a tire truing machine. But removing tread obviously reduces the remaining service life of the tire, so this approach would not be recommended unless the runout can be eliminated with minimal tread removal.
Lateral runout on the tire should also be checked. If more than .050 inches, measure lateral runout in the wheel and compare the two to determine which one has the problem. If the wheel is within specifications but the tire is not, the tire has too much runout and needs to be replaced.
With wheels, the amount of lateral and radial runout that’s acceptable will vary according to the application. Alloy wheels on small cars with MacPherson strut suspensions are much more sensitive to both kinds of runout than steel wheels on larger rear-wheel drive vehicles. If lateral (sideways) or radial (vertical) runout exceed specifications, the wheel should be replaced.
As a rule, a wheel with .050 inches or more of radial runout, or is more than .025 to .035 inch out-of-round can cause problems. Lateral runout may be excessive if it exceeds .035 inches on a steel rim, or .020 inches on an alloy rim. Some vehicles are so sensitive to lateral runout that a difference of only .008 to .010 inches side-to-side can cause a noticeable vibration in the steering.
The only cure for a wheel with too much runout is to replace it (though there are aftermarket services that can straighten and repair expensive alloy wheels).
Radial runout on a vehicle can sometimes be reduced be reindexing the wheel on the hub. Another option is to install a tapered correction shim between the hub and rotor to offset the runout. If moving the wheel one or two lug positions fails to reduce runout, and it cannot be corrected with a shim, the hub should be replaced. As a rule, hub runout as measured at the lugs should not vary more than .030 inch.
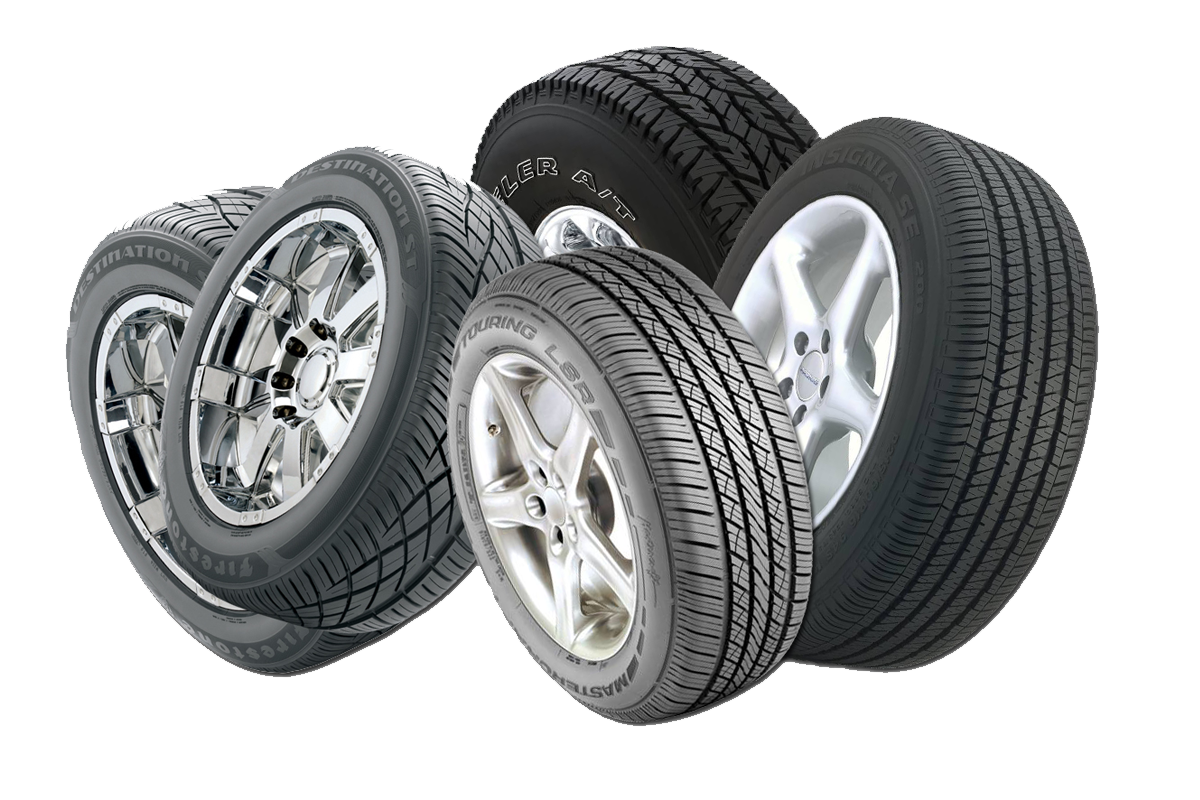
Diagnosing Tire Problems
by
Tags:
Leave a Reply