As components of automobiles, oxygen sensors have existed for more than 20 years. However, a majority of car drivers do not even know them, let alone their function.
The only time most people even become aware of an oxygen sensor’s existence is if they get a Check Engine light and there is a code that indicates an O2 sensor problem or their vehicle fails an emissions test because of a sluggish or dead O2 sensor. If their engine is not running well or is using too much fuel, somebody might tell them they might need a new O2 sensor. But in most cases, they will not have a clue as to how to diagnose or test this mysterious little device that is often blamed for all kinds of driveability and emissions ills.
An O2 sensor monitors the fuel mixture so the engine computer (Powertrain Control Module) can adjust the air/fuel ratio to maintain the lowest possible emissions and best fuel economy. The O2 sensor does this by reacting to unburned oxygen in the exhaust. The sensor generates a small voltage signal (usually less than 1 volt) that increases when the air/fuel mixture goes rich, and drops when the air/fuel mixture goes lean. It acts like a rich/lean switch that signals the computer every time the fuel mixture changes, which is constantly.
The computer maintains a balanced fuel mixture by doing the opposite of what the O2 sensor reads. If the O2 sensor reads rich (too much fuel), the computer shortens the on-time of each injector pulse to reduce the amount of fuel being squirted into the engine. This makes the mixture go lean. As soon as the O2 sensor detects this and gives a lean reading (not enough fuel), the computer reacts and increases the on-time of each injector pulse to add more fuel. This back-and-forth balancing act creates an average mixture that is pretty close to ideal. This is the “fuel feedback control loop” that allows today’s vehicles to maintain extremely low emissions levels, and the O2 sensor is the key sensor in this loop.
The computer uses other sensor inputs, too, like those from the coolant sensor, throttle position sensor, manifold absolute pressure sensor, airflow sensor, etc. to further refine the air/fuel radio as needed to suit changing operating conditions. But the O2 sensor provides the main input that determines what happens to the fuel mixture. So if the O2 sensor is not reading right, it screws up everything.
Typically, a bad O2 sensor will read low (lean), which causes the engine to run too rich, pollute too much and use too much gas. A low reading can be caused by several things: old age, contamination, a bad wiring connection, or an ignition or compression problem in the engine.
Getting Old
As an O2 sensor ages, it does not react as quickly as it once did. The increased lag time makes the sensor sluggish and prevents the engine from keeping the air/fuel mixture in close balance. If the engine burns oil or develops an internal coolant leak, the sensor element may become contaminated causing the sensor to fail. Back when leaded gasoline was still available, a single tankful of leaded fuel would kill most O2 sensors in a few hundred miles. (That is a main reason why the government finally eliminated leaded fuel.)
Because the sensor reacts to oxygen in the exhaust and not fuel, any engine problem that allows unburned air to pass through the cylinders will also trick an O2 sensor into reading lean. A misfiring spark plug or a leaky exhaust valve – even a leak in the exhaust manifold gasket – may allow enough air into the exhaust to screw up the sensor readings. It won’t damage the sensor, but it will create a rich running condition that hurts emissions and fuel economy.
Getting Hot
Something else you need to know about O2 sensors is that they have to be hot (617 degrees to 662 degrees F) to produce a voltage signal. It may take a few minutes for the exhaust to heat up the sensor, so most O2 sensors in newer vehicles have a built-in electrical heater circuit to get the sensor up to temperature as quickly as possible. These are usually three-wire and four-wire O2 sensors. The single- and two-wire O2 sensors are unheated.
If the heater circuit fails, it will not affect the operation of the O2 sensor once the exhaust gets hot but it will delay the computer from going into closed loop, which may cause a vehicle to fail an emissions test.
Getting Checked Out
O2 sensors can be diagnosed a variety of ways, most of which require special equipment. A scan tool or code reader is required to pull trouble codes from most newer vehicles, though manual “flash codes” are available on older vehicles (pre-1995). If an O2 sensor problem is suspected, the sensor’s response and voltage output can be monitored with a scan tool, a voltmeter or digital oscilloscope. If the tests confirm the O2 sensor is dead or sluggish, replacement is the only repair option. There is no way to “clean” or “rejuvenate” a bad O2 sensor.
Note: Replacement sensors must be the same basic type as the original (heated or unheated) and have the same performance characteristics and heater wattage requirements. Installing the wrong O2 sensor could affect engine performance and possibly damage the heater control circuit in the engine computer. So make sure you follow the O2 sensor supplier’s replacement listings.
And do not go by appearance alone. Some replacement O2 sensors have an OEM-type wiring connection and require no modifications to install. Others (typically the “universal type O2 sensors”) require splicing the sensor wires into the original connector harness.
When to Replace Oxygen Sensors
To maintain peak engine performance, there is no need to wait until the sensor fails to replace it. Some experts now recommend replacing O2 sensors at specific mileage intervals for preventive maintenance. The recommended interval for unheated one- or two-wire O2 sensors on 1976 through early 1990s applications is every 30,000 to 50,000 miles. Heated three- and four-wire O2 sensors on mid-1980s through mid-1990s applications can be changed every 60,000 miles. And on 1996 and newer OBD II vehicles, the recommended replacement interval is 100,000 miles.
Knowing What Type Is Used
The most common zirconia type O2 units all work the same, but there are also titania O2 sensors and “wide-band” O2 sensors. Unheated zirconia O2 sensors are the oldest type. They have one or two wires and take up to several minutes to generate a signal after a cold start because they rely solely on the heat from the exhaust to reach normal operating temperature. Consequently, an unheated sensor may cool off at idle and stop producing a signal causing the engine control system to revert back to “open loop” operation (fixed air/fuel ratio setting).
In 1982, heated zirconia O2 sensors appeared that added a special heater circuit inside the sensor to bring it up to operating temperature more quickly (in 30 to 60 seconds). This allows the engine to go into closed loop sooner, which reduces cold-start emissions. It also prevents the sensor from cooling off at idle. The heater requires a separate electrical circuit to supply voltage, so heated sensors usually have three or four wires.
Titania O2 sensors use a different type of ceramic and produce a different kind of signal than zirconia type O2 sensors. Instead of generating a voltage signal that changes with the air/fuel ratio, the sensor’s resistance changes and goes from low (less than 1,000 ohms) when the air/fuel ratio is rich to high (more than 20,000 ohms) when the air/fuel ratio is lean. The switching point occurs right at the ideal or stoichiometric air/fuel ratio. The engine computer supplies a base reference voltage (1 volt or 5 volts, depending on the application), and then reads the change in the sensor return voltage as the sensor’s resistance changes. Titania O2 sensors are only used on a few applications, including some older Nissan and 1987-1990 Jeep Cherokee, Wrangler and Eagle Summit models.
In 1997, some vehicle manufacturers began using a new type of O2 sensor. The heated planar O2 sensor has a flat, ceramic zirconia element rather than a thimble. The electrodes, conductive layer of ceramic, insulation and heater are all laminated together on a single strip. The new design works the same as the thimble-type zirconia sensors, but the “thick-film” construction makes it smaller, lighter and more resistant to contamination. The new heater element also requires less electrical power and brings the sensor up to operating temperature in only 10 seconds.
Some new vehicles are also using a wide-band O2 sensor that is similar to the planar design but produces a higher voltage signal that changes in direct proportion to the air/fuel ratio (instead of switching back and forth like the other types of O2 sensors). This allows the engine computer to use an entirely different operating strategy to control the air/fuel ratio. Instead of switching the air/fuel ratio back and forth from rich to lean to create an average balanced mixture, it can simply add or subtract fuel as needed to maintain a steady ratio of 14.7:1.
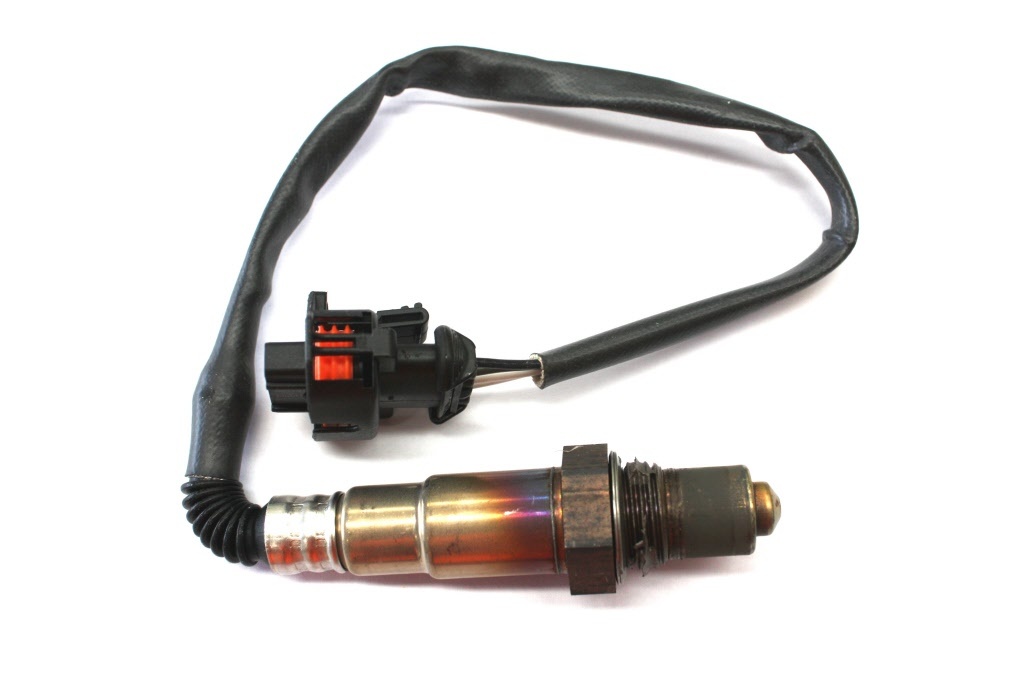
Oxygen sensors can be the one to blame in automotive emission problems
by
Tags: